Conversion of high power usually requires high currents. This means that the core of an inductor or transformer must be physically large to avoid high magnetic flux that will saturate the magnetic material. I will need such a core for the most recent design concept. Small ferrite cores can be found on the surplus market, but something in the 3-inch-and-up range is hard to come by. I could get a brand new one from a place like Mouser, but would have to pay upwards of $100. But look what I found in the bargain bin at Halted:
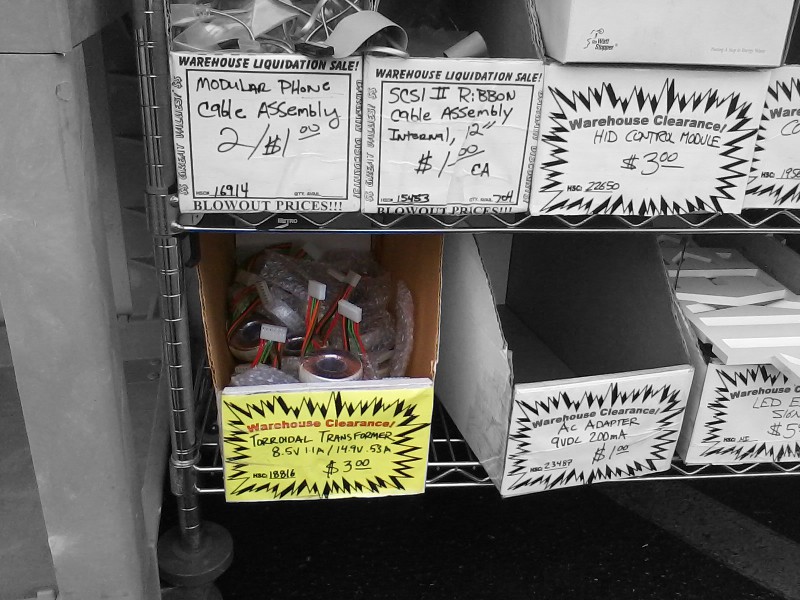
My thought was to harvest the (hopefully ferrite) core from one of these transformers, and re-wind my own.
At the bargain bin, I had no way of knowing what the cores inside the transformers would be like. For all I knew, they could have been rings of rusty cast iron. I suppose that if I had a magnet handy, I could have tested for attraction. Or if I had my inductance meter, I could have wound a single loop of wire onto the toroid to measure AL. Naturally, I had neither of those on hand. But hey, the parts were cheap, and the education would be worth it no matter what. I bought two.
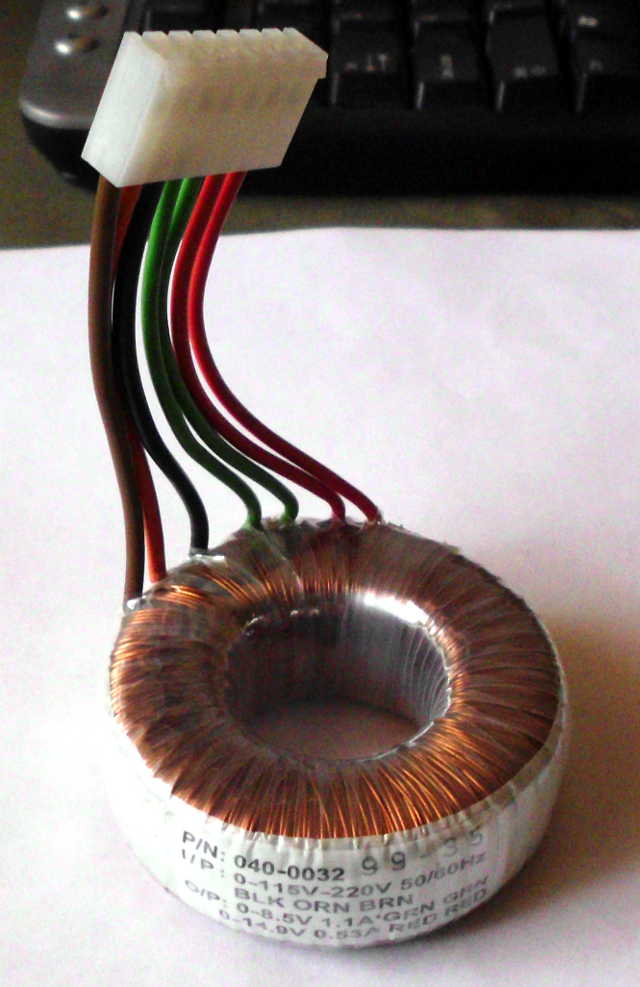
At home, I was able to put a loop (actually, a few loops) of wire around the toroid, measure the inductance, and calculate AL. I came up with a value of 2.5 μH. Encouraging.
I was initially worried that the whole assembly might be potted in epoxy or varnished in place. Thankfully, this was not the case – everything was held together by tape, which was easily removed.
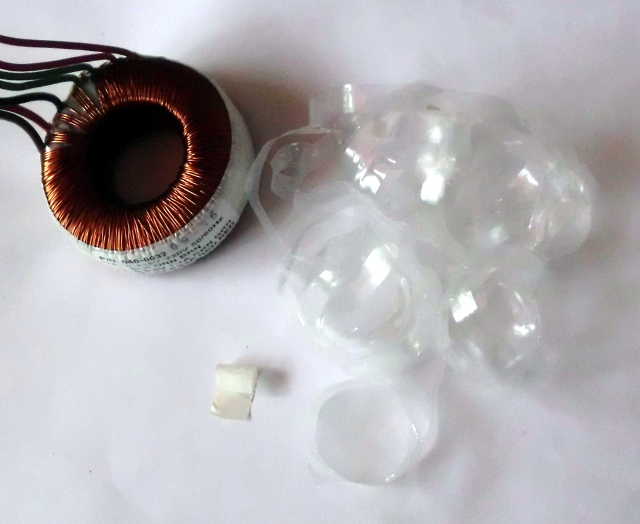
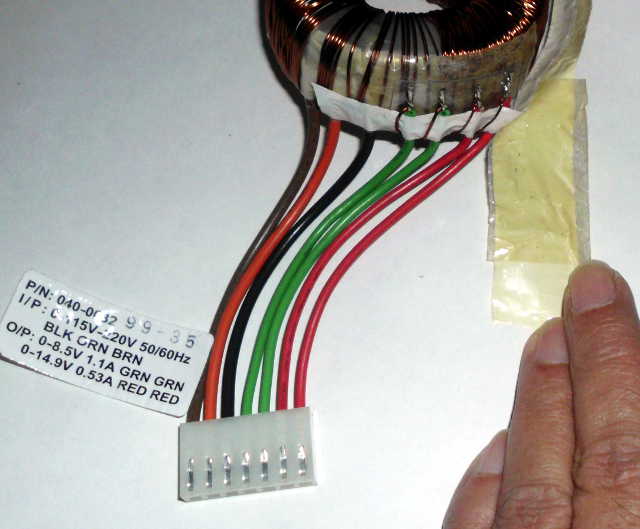
The first thing I unwound was the the lowest voltage secondary. I was surprised by how many turns there were for just 8.5 volts. Previously, I had measured the inductance of this winding at 43.9 mH, and since inductance is proportional to the square of the number of turns, it would have been possible to calculate in advance that there were about 133 turns. The wire was a nice #20 or so, which I thought I might be able to reuse later.
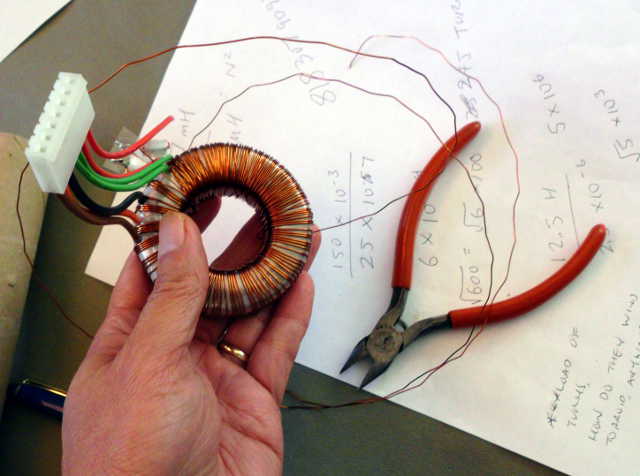
For reasons to be explained later, the maximum number of turns of #20 I would need per secondary in the rewound transformer was 12, so I unwound 15 turns at a time before cutting off a length of wire. Why cut it at all? Because it would have taken a prohibitively long time to remove the long wire in one piece. In fact, I’m amazed at how the manufacturer can wind hundreds or thousands of turns onto a toroid. What kind of machine must they use?
Unwinding the secondaries took hours. Then came the really hard job – unwinding the primary. The primary was center-tapped, and across the ends had an inductance of 12.35 Henries, which translated to about 2200 turns. The primary seemed to be #34 or so wire – too fine to be useful to me – so I could have just cut it off. But I was concerned about damaging the core. And further, I wanted to be responsible and recycle the copper, so didn’t want a lot of copper dust and fragments. That meant days of manual unwinding, about 5 feet at a time.
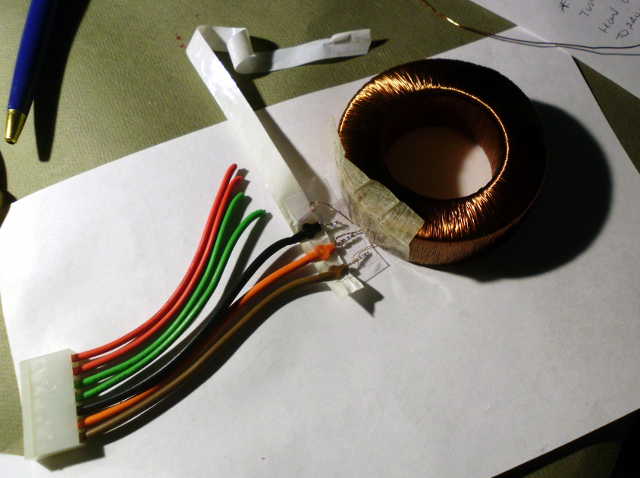
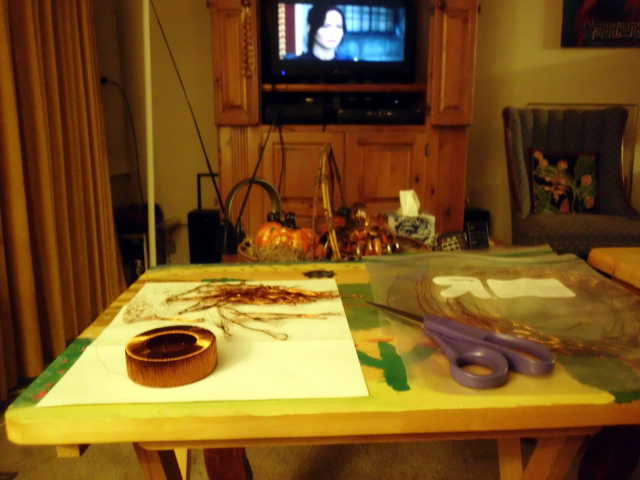
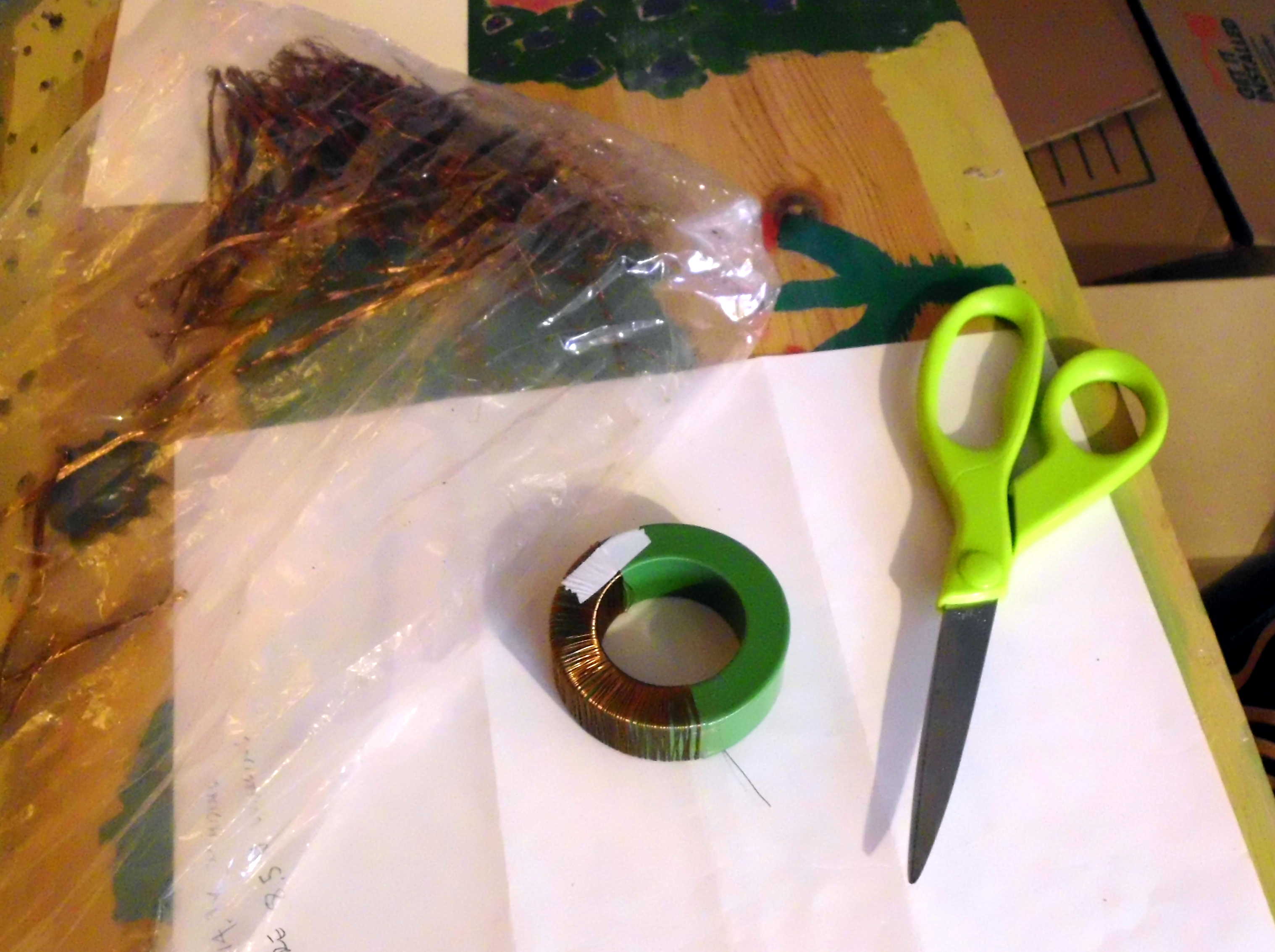
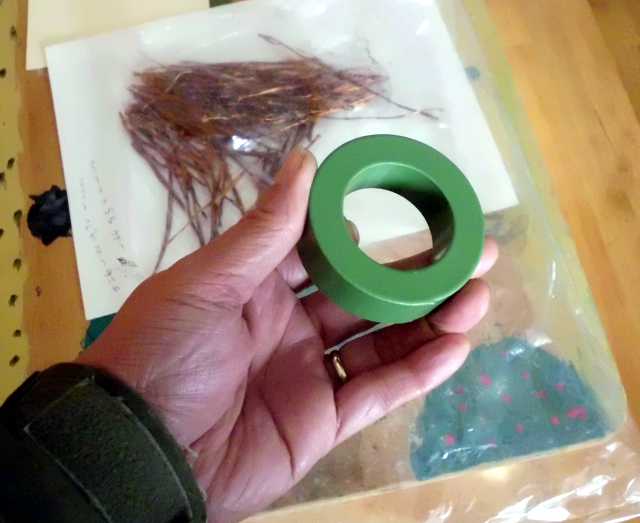